Bugatti Develops World's First Brake Caliper By 3-D Printer
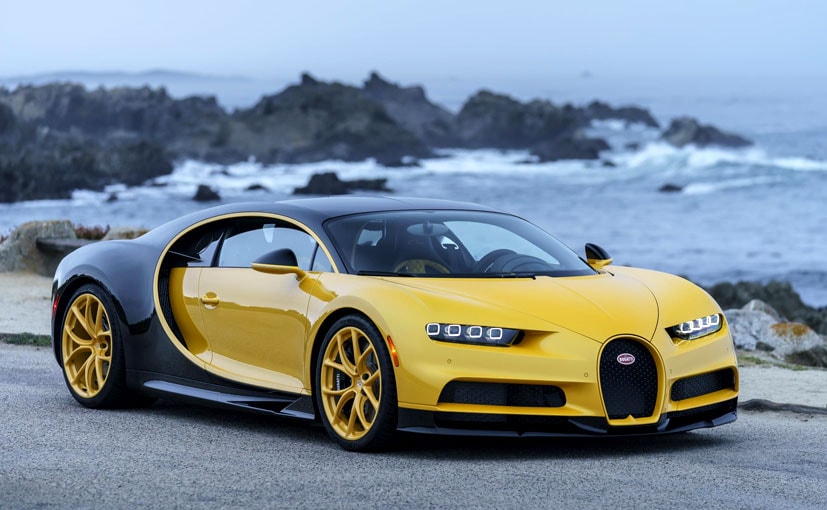
Highlights
The Development Department of Bugatti, for the first time, has developed a brake caliper that can be produced by 3-D printing. While the main material used for the additive production of vehicle components to date has been aluminum; the new brake caliper is made from titanium, making it the world's largest functional component produced from titanium using 3-D printing processes. The French car-makers collaborated with Laser Zentrum Nord of Hamburg to develop these new brake calipers, who have been working on this since the beginning of the year. Vehicle trials for the use of the 3-D titanium brake caliper in series production are to start in the first half of the year.
Also Read: Bugatti Announces Worldwide Recall Of Chiron. Here's Why
Frank Gotzke, Head of New Technologies, Technical Development Department, Bugatti Automobiles S.A.S said, "Vehicle development is a never-ending process. This is particularly true at Bugatti. In our continuing development efforts, we are always considering how new materials and processes can be used to make our current model even better and how future vehicles of our brand could be designed."
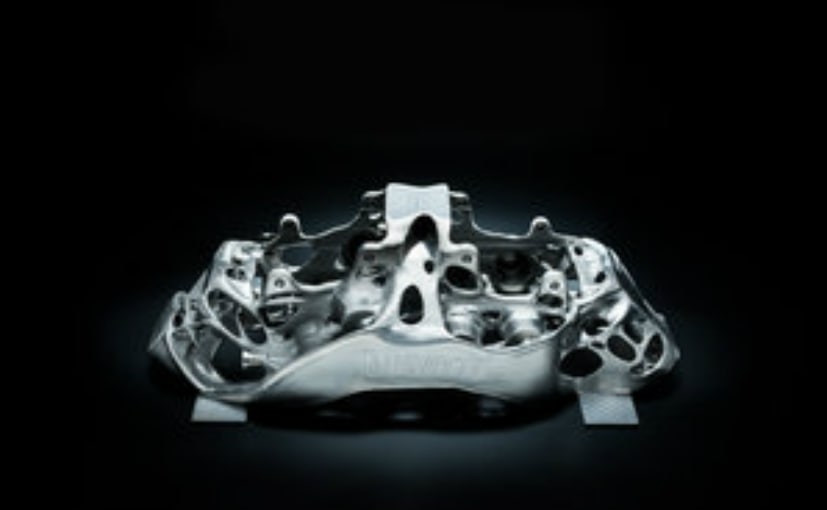
(Bugatti currently uses the most powerful brakes in the world on the new Chiron)
Bugatti currently uses the most powerful brakes in the world on the new Chiron. The brake calipers were an entirely new development. They are forged from a block of high-strength aluminum alloy. With eight titanium pistons on each of the front calipers and six on each of the rear units, these are also the largest brake calipers currently installed on a production vehicle. The brake calipers of the Chiron are produced using bionic principles on the basis of a natural model. The new architecture combines minimum weight with maximum stiffness. The new titanium brake caliper weighs about 2.9 kg, while the aluminum component currently used, weighs 4.9 kg.
Also Read: Bugatti Chiron Sets World Record In Under 42 Seconds
Gotzke added, "In terms of volume, this is the largest functional component produced from titanium by additive manufacturing methods. Everyone who looks at the part is surprised at how light it is - despite its large size. Technically, this is an extremely impressive brake caliper, and it also looks great."
The development time for the 3-D-printed titanium brake caliper took about three months, from conceptualizing to the production of first printed component. The basic concept was sent to Laser Zentrum Nord as a complete data package. They then carried out the process simulation, the design of the supporting structures, actual printing and the treatment of the component. Bugatti was responsible for finishing.