How Is A Formula 1 Car Made?

Highlights
- Critical attention is required every step of the making process
- Workers wear special coveralls and shoes during production
- The chassis goes through several tests before it is fitted in F1 cars
The Formula 1 team engineers use Finite Element, CAD, and Stress Analysis software to analyze, design, and refine the chassis and the overall car mechanisms. The leading proponents of the chassis are the fuel tanks, roll structures, ballasts, and survivors.
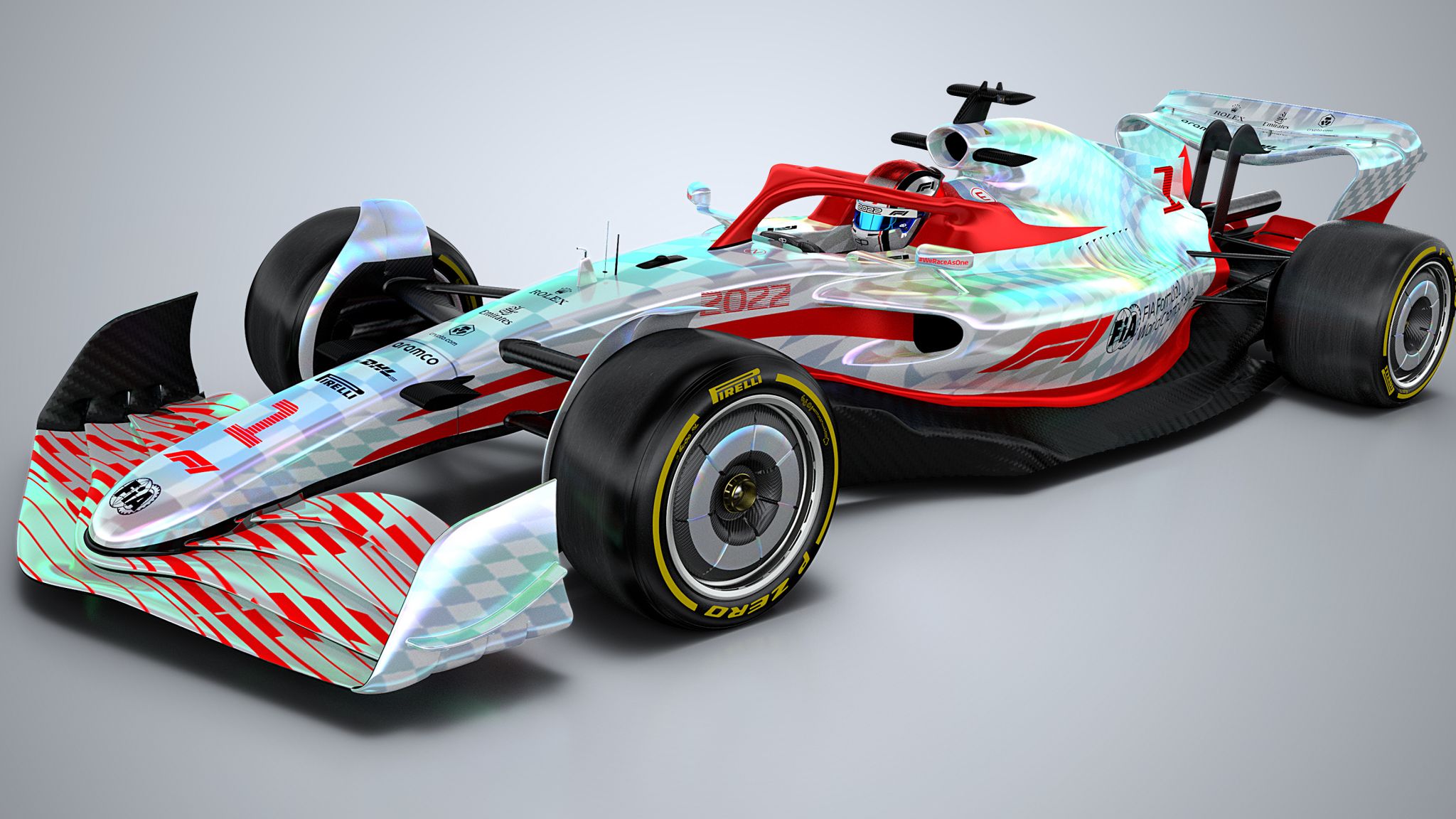
Photo Credit: www.formula1.com
The five-axis milling machine cuts out the solid epoxy chassis. The milling machine gathers and reads the data from the CAD files to replicate and deliver the contours and dimensions specified in the patterns. If there are any defects found in the patterns of the files, then the chassis will be reproduced as it is a critical part, and the patterns need to be made perfectly and defect-free.
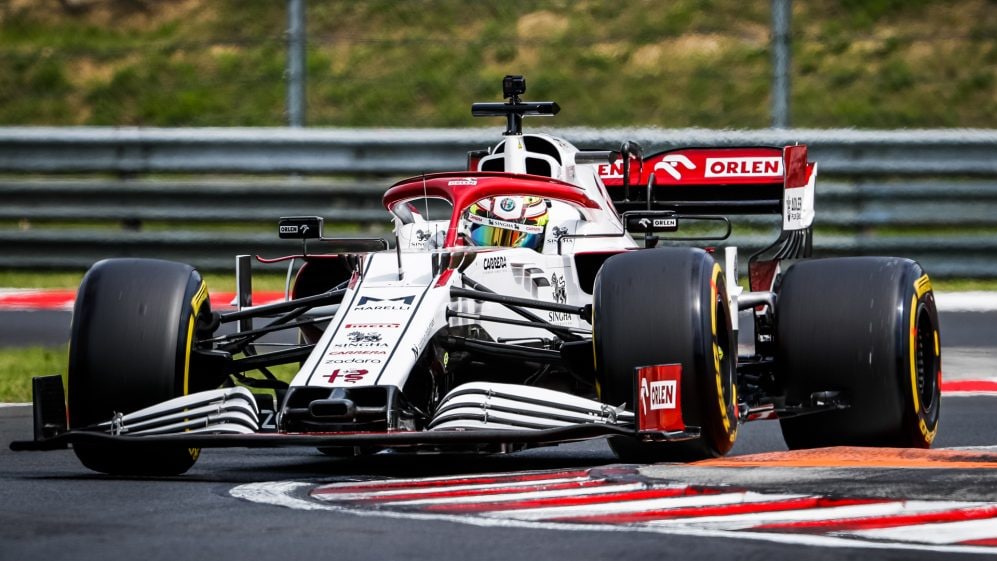
Photo Credit: www.formula1.com
Inside the Production:
Engineers use epoxy instead of metals to reduce thermal expansion when the moulds are subjected to extremely high temperatures during the curing process. Production ensues in the cleanroom, which is sealed by double-door airlocks. The environment has to be tightly controlled, and the workers wear shoes and specially designed coveralls at all times.
Carbon fibre is used to construct the moulds, and the process has several stages. Vacuum treatments, layering, and thermal curing are a few processes that the moulds undergo. Upper and lower moulds are bonded together, and these two are used in halves. Extreme caution is taken in the production process not to damage any of these parts.
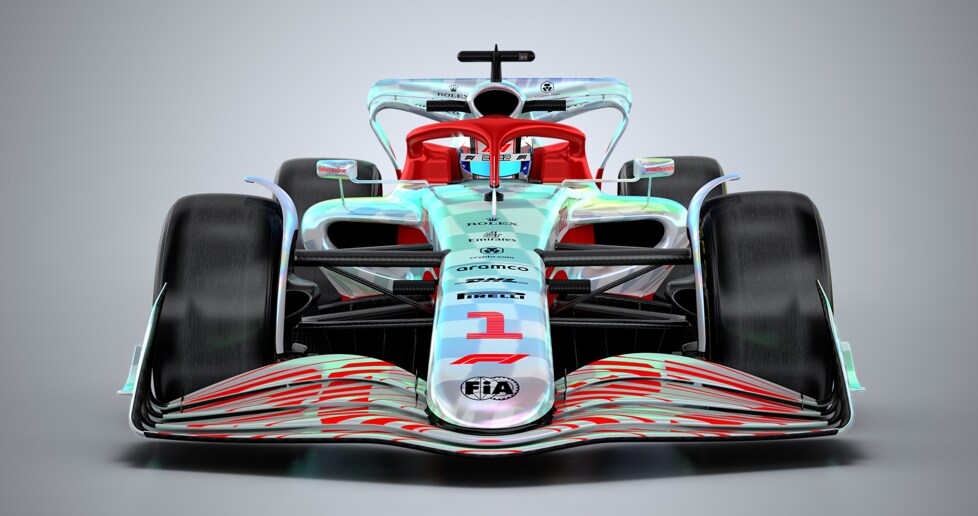
Photo Credit: www.formula1.com
Carbon Fiber is the Way to Go:
The chassis is made from carbon fibre, and several other fibre types are used. The orientation of the plies is critical as they are to be aligned in specific directions to accommodate the requirements. The orientation and the number of plies used vary from location to location in and around the chassis. Additional plies are needed for high-stress areas, such as the suspension mounting points and the engine, to give you some perspective.
Workers use reference manuals containing visual descriptions of how the plies should be applied to ensure the correct critical positioning of the plies. Once the ply gets layered, an inspecting officer checks the manual and gives his approval before moving on to the next ply. Once the plies are laid out in the correct position in the mould, the entire stack is put in a vacuum bag, which is further placed in an autoclave. The bag then vacuums down so that the plies get squeezed together.
Resin & the Final Process
The plies contain resin, and the high temperatures in the autoclave cause it to flow throughout the fabric evenly. The two halves of the chassis are taken out of their moulds and are then glued together to form a single solid shell. The bulkheads get glued to the shell to provide mountings for the suspension rockers at the front and the seatback of the driver. The final trimming and machining process occurs, and special attention is required at every step of the way.
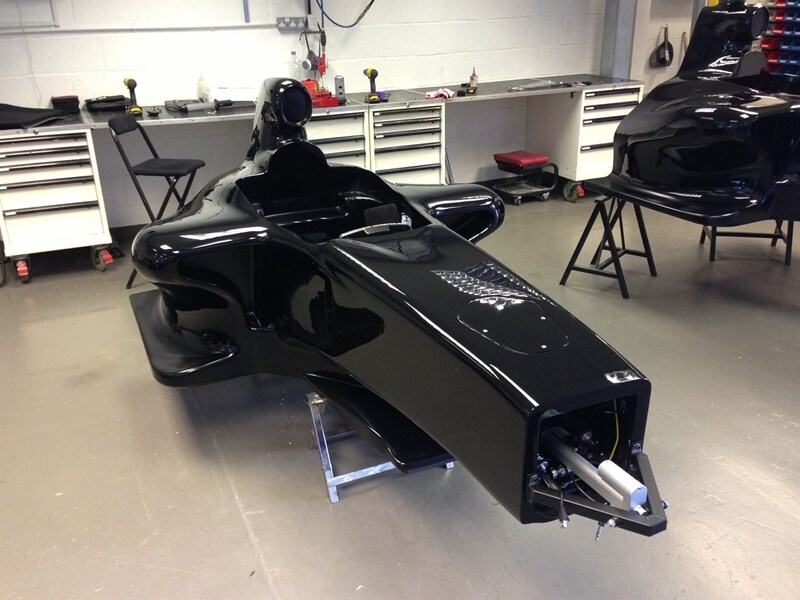
Photo Credit: lifebeyondsportmedia.com
After the chassis is made, it must go through several crash tests conducted by the FIA before a designated official. Once the official approves the chassis, the car is permitted to run on the track.