Ford Teams Up With HP To Transform 3D Printing Waste Into Auto Parts

Highlights
Ford is continuing to drive the future of automotive 3D printing, this time teaming up with HP to reuse spent 3D printed powders and parts, turning them into injection moulded vehicle parts - an industry first. The resulting injection moulded parts are better for the environment with no compromise in the durability and quality. The recycled materials are being used to manufacture injection-moulded fuel-line clips installed first on Super Duty F-250 trucks.
The parts have better chemical and moisture resistance than conventional versions, are 7 per cent lighter and cost 10 per cent less. The Ford research team has identified 10 other fuel-line clips on existing vehicles that could benefit from this innovative use of material and are migrating it to future models.
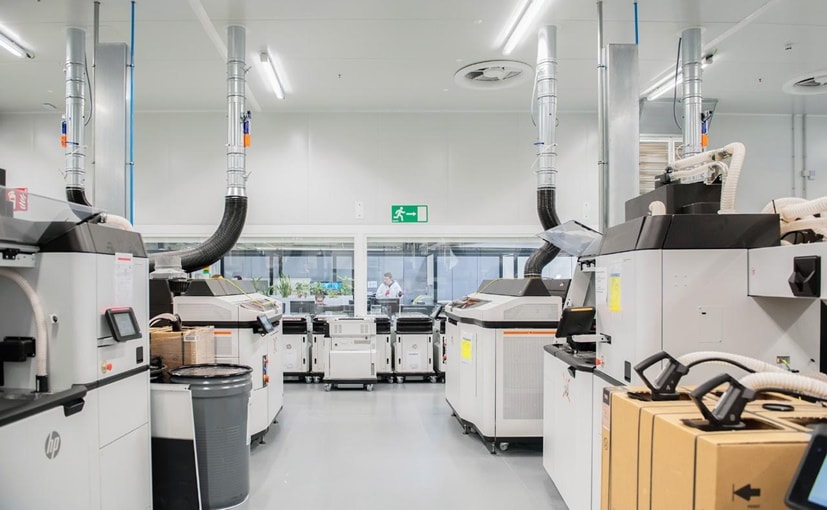
The parts have better chemical and moisture resistance than conventional versions, are 7 per cent lighter and cost 10 per cent less
HP 3D printers are already designed for high efficiency, with systems and structures to minimize the excess material they generate and reuse a greater percentage of the materials put into them. Working with Ford, which uses HP's 3D printing technology at the company's Advanced Manufacturing Centre, the team created this solution that produces zero waste.
For its part, Ford is developing new applications and utilizing a multitude of different processes and materials for 3D printing, including filaments, sand, powders and liquid vat polymerization. The company already employs 3D printing for a variety of low-volume commercial vehicle parts, as well as fixtures used by assembly line workers, saving time and enhancing quality. Companywide, Ford has a goal to achieve 100 per cent sustainable materials in its vehicles.
Related Articles
Latest News
- Home
- News
- Auto Industry
- Ford Teams Up With HP To Transform 3D Printing Waste Into Auto Parts